
Crusher Types: A Comprehensive Guide
Crusher Types: A Comprehensive Guide
Crusher are machines used to reduce the size of rocks, stones, and ore. They are used in a variety of industries, including mining, construction, and demolition. Crushers use mechanical force to break down large rocks into smaller, more manageable pieces.
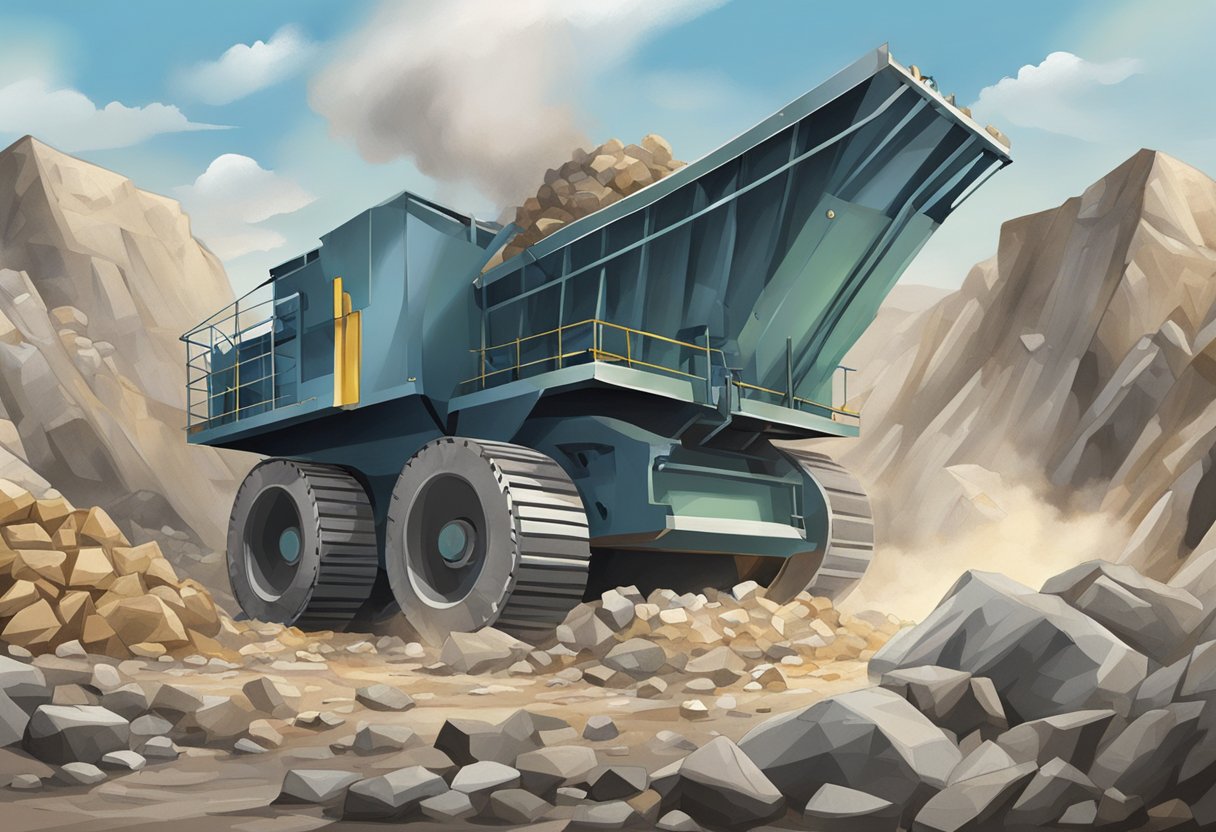
The primary purpose of crushers is to reduce the size of the material for further processing. Crushers can be used to produce smaller particles for use in construction materials like concrete and asphalt. They can also be used to crush ore for processing in mining operations.
Crushers come in a variety of types, including jaw crushers, Vacuum Pump Unit cone crushers, and impact crushers. Each type of crusher is designed to work with a certain maximum size of raw material and often delivers its output to a screening machine which sorts and directs the product for further processing. Different types of crushers are used depending on the type of material being crushed and the desired output size.
Types of Crushers
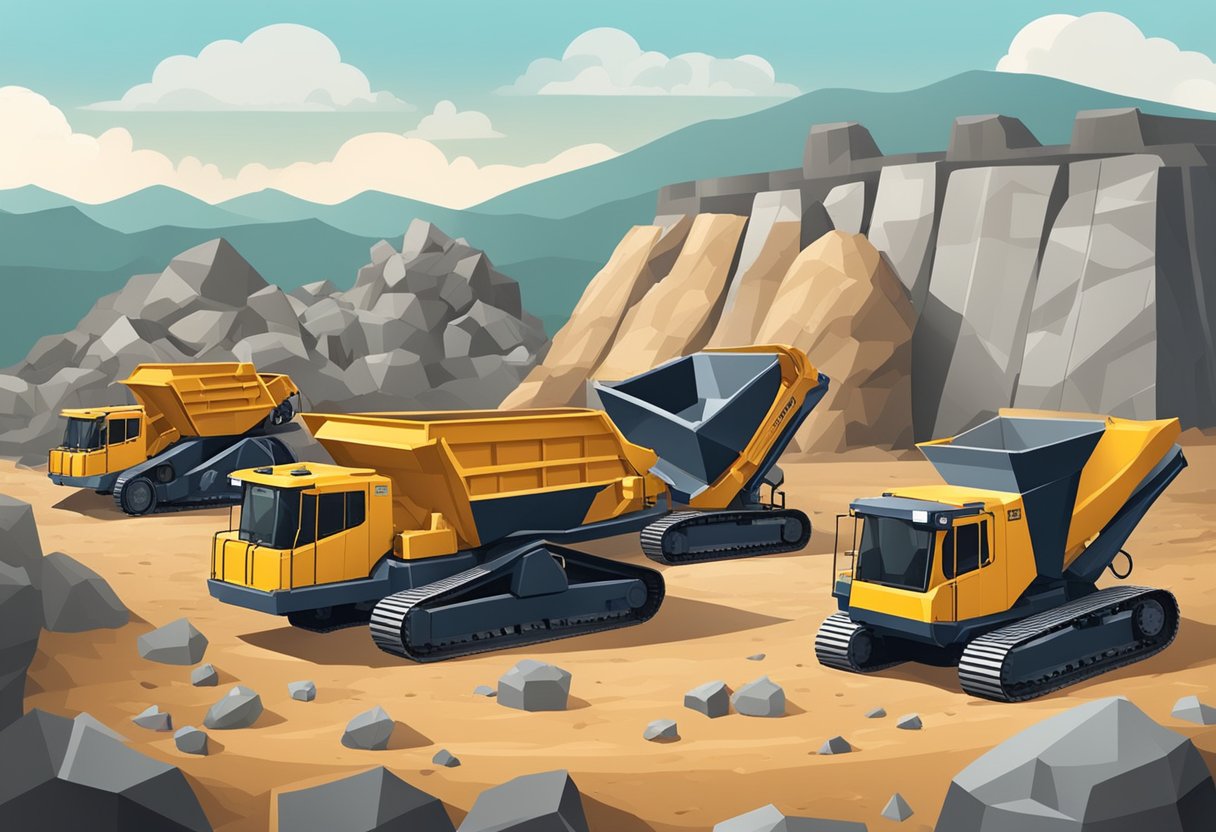
Jaw Crusher
A Jaw Crusher is one of the most commonly used primary crushers. It uses a compressive force to crush the material between two plates. The movable jaw plate pivots at the top and is pulled towards the fixed jaw plate, which is stationary. The material is crushed as it passes through the gap between the two plates.
Cone Crusher
A Cone Crusher is used for secondary crushing. It uses a rotating mantle and a stationary concave to crush the material. The material is fed into the top of the cone crusher and is crushed as it falls down on the mantle. The size of the crushed material can be adjusted by changing the gap between the mantle and the concave.
Impact Crusher
An Impact Crusher is used for crushing of soft materials like limestone, coal, and clay. It uses a high-speed rotor to impact the material and break it into smaller pieces. The material is fed into the machine through a feed chute and is hit by the rotor’s hammers. The crushed material is then discharged through an opening at the bottom of the machine.
Gyratory Crusher
A Gyratory Crusher is used for primary crushing. It consists of a concave surface and a conical head. The material is fed into the top of the machine and is crushed as it falls down on the conical head. The gyratory crusher has a high capacity and can handle large rocks.
Roll Crusher
A Roll Crusher is used for secondary crushing. It consists of two rollers with parallel axes. The material is fed into the top of the machine and is crushed between the rollers as they rotate in opposite directions. Roll crushers are used for smaller size reduction requirements and are often used in laboratories.
In summary, there are various types of crushers available for different applications. Each type of crusher has its advantages and disadvantages. It is important to choose the right type of crusher for the specific application to achieve the desired results.
Industrial Applications
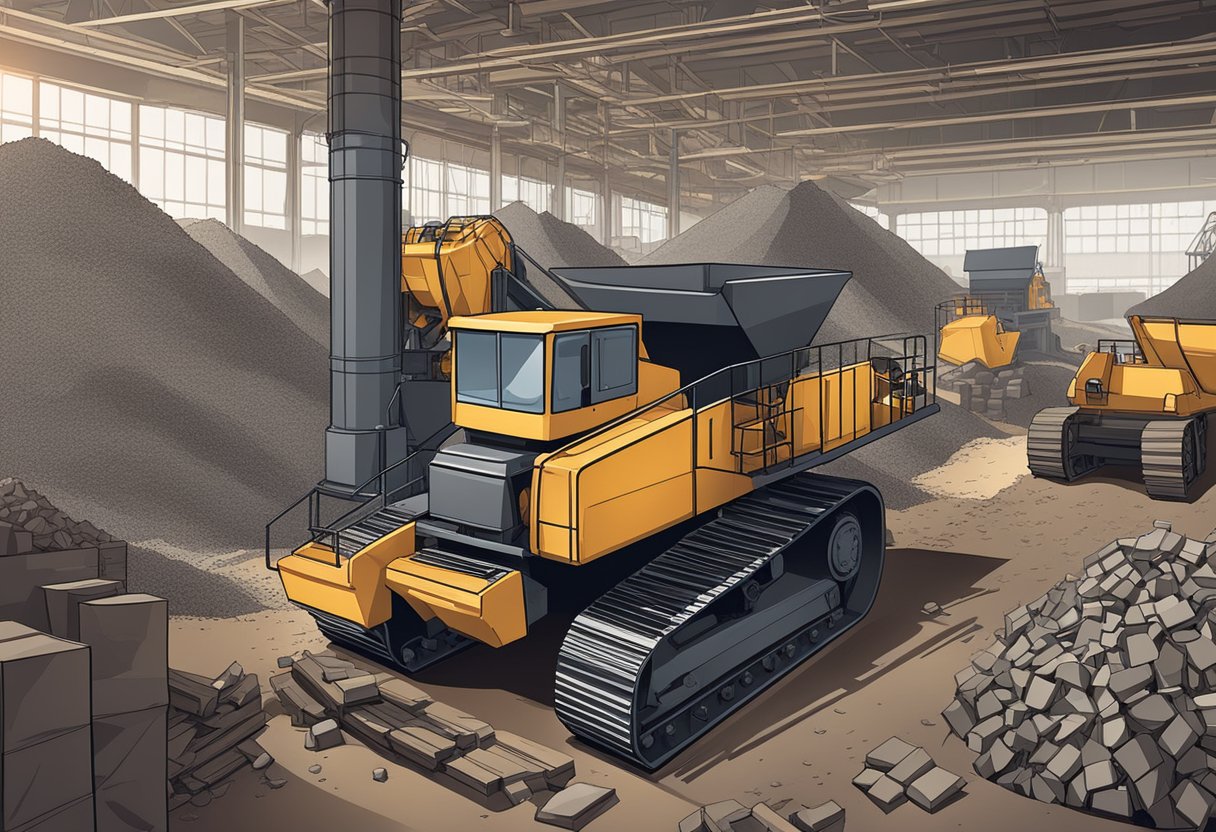
Crushers are widely used in various industrial applications due to their ability to break down large, solid materials into smaller pieces. This section highlights some of the key industrial applications of crushers.
Mining Industry
In the mining industry, crushers are used to crush and grind rocks and ores for further processing. Crushers are essential for the mining industry as they help in reducing the size of the extracted mineral or metal. This makes the transportation of the extracted material easier and more efficient. Crushers used in the mining industry include jaw crushers, cone crushers, and gyratory crushers.
Aggregate Production
Crushers are also used in the aggregate production industry to break down large rocks into smaller pieces. The smaller pieces can then be used as construction materials such as concrete and asphalt. Crushers used in the aggregate production industry include impact crushers, cone crushers, and jaw crushers.
Recycling Operations
Crushers are crucial in recycling operations as they help in reducing the size of waste materials. This makes it easier to transport and recycle the waste materials. Crushers used in recycling operations include impact crushers, jaw crushers, and cone crushers.
Overall, crushers have a wide range of industrial applications, and their importance cannot be overstated. They are essential in various industries, including mining, aggregate production, and recycling operations.
Crushing Principles
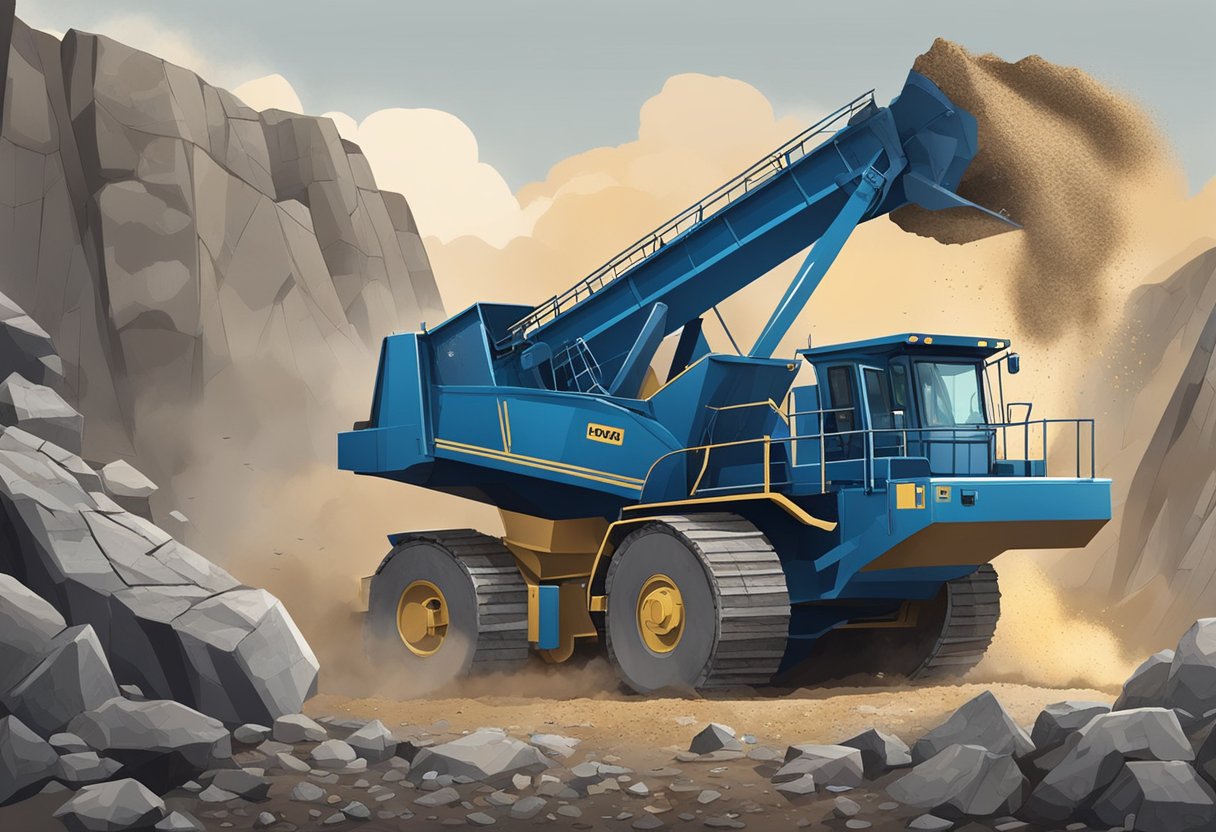
Crushing is the process of reducing the size of solid materials into smaller pieces by applying mechanical force. There are three main types of crushing principles: compression crushing, impact crushing, and shear crushing.
Compression Crushing
Compression crushing involves applying a force to the material to crush it by squeezing the material between two surfaces. This type of crushing is commonly used in the mining industry to crush hard materials such as granite, limestone, and iron ore. The material is fed into the crusher and is crushed between the mantle and the bowl liner or concave. The size of the crushed material is determined by the gap between the mantle and the bowl liner.
Impact Crushing
Impact crushing involves the use of a rotating rotor to strike the material and break it into smaller pieces. This type of crushing is commonly used in the recycling industry to crush concrete, asphalt, and other construction materials. The material is fed into the crusher and is struck by the rotor, which rotates at high speed. The impact causes the material to break into smaller pieces, which are then discharged through the bottom of the crusher.
Shear Crushing
Shear crushing involves the use of two or more blades to cut the material into smaller pieces. This type of crushing is commonly used in the food industry to crush fruits, vegetables, and other soft materials. The material is fed into the crusher and is cut by the blades, which rotate at high speed. The size of the crushed material is determined by the gap between the blades.
In conclusion, understanding the principles of crushing is essential for selecting the right crusher for a specific application. Each type of crushing has its own advantages and disadvantages, and the appropriate type of crushing should be selected based on the material properties and the desired end product.
Design and Operation
Machine Components
A crusher is typically composed of several main components, including the frame, the rotating element, the crushing mechanism, and the discharge mechanism. The frame serves as the support structure for the other components and is usually made of steel or cast iron. The rotating element, typically a shaft or drum, houses the crushing mechanism and is powered by an electric motor or other source. The crushing mechanism itself can vary depending on the type of crusher, but typically consists of a series of jaws or cones that apply pressure to the material being crushed. Finally, the discharge mechanism allows the crushed material to exit the crusher and can be designed to include features such as a conveyor belt or chute.
Crusher Assembly
The assembly process for a crusher can vary depending on the manufacturer and specific model, but typically involves several stages. First, the main components are fabricated and assembled into the frame. Next, the rotating element and crushing mechanism are added, followed by the discharge mechanism. Finally, any necessary electrical components are installed and the crusher is tested to ensure proper operation.
Operational Parameters
The operational parameters for a crusher can also vary depending on the specific model and application. These parameters can include the feed rate, the size and type of material being crushed, the speed of the rotating element, and the gap between the crushing surfaces. Proper adjustment of these parameters is critical to ensuring optimal performance and minimizing wear on the crusher components. Additionally, proper maintenance and lubrication of the crusher can help extend its lifespan and ensure reliable operation.
Material Characteristics
Hardness
The hardness of the material being crushed is an important factor to consider when selecting a crusher. Harder materials may require a tougher and more durable crusher to withstand the high pressure and impact of the crushing process.
Crushers are typically designed to handle materials with a maximum hardness of around 320 MPa. However, some crushers are capable of crushing harder materials such as granite, basalt, and quartz up to 600 MPa.
Abrasion Index
The abrasion index of the material being crushed is another important factor to consider. The abrasion index is a measure of how resistant the material is to wear and tear during the crushing process.
Materials with a high abrasion index may cause excessive wear and tear on the crusher, resulting in higher maintenance costs and reduced lifespan. Therefore, it is essential to select a crusher that can handle the abrasiveness of the material being crushed.
Moisture Content
The moisture content of the material being crushed can also impact the performance of the crusher. Moisture can cause the material to clog or stick together, reducing the efficiency of the crushing process.
Materials with high moisture content may require additional drying or pre-processing before being fed into the crusher. It is important to select a crusher that can handle the moisture content of the material being crushed to ensure optimal performance.
Crusher Selection
When selecting a crusher, it is important to consider various factors to ensure that the crusher meets the requirements of the application. The following subsections outline some of the key factors to consider when selecting a crusher.
Capacity Requirements
One of the most important factors to consider when selecting a crusher is the required capacity. The capacity of the crusher should be sufficient to handle the maximum expected throughput of the application. It is important to ensure that the crusher can handle peak loads without causing downtime or damage to the equipment.
Material Properties
The properties of the material being processed are also important when selecting a crusher. The hardness, abrasiveness, and moisture content of the material can all affect the performance of the crusher. For example, a material that is very hard may require a crusher with a higher horsepower rating to achieve the desired output.
Output Size
The desired output size of the material is another important factor to consider when selecting a crusher. The crusher should be capable of producing the desired output size with minimal oversize material. It is important to note that the output size may vary depending on the type of crusher and the settings used.
In summary, selecting the right crusher requires careful consideration of various factors, including capacity requirements, material properties, and output size. By taking these factors into account, it is possible to select a crusher that will meet the needs of the application and provide reliable performance.
Maintenance and Safety
Maintenance Strategies
Proper maintenance of a crusher is essential for its optimal performance and longevity. Here are some maintenance strategies that can help ensure the crusher operates smoothly:
- Regularly inspect and replace worn-out parts: Worn-out parts such as liners, jaws, and hammers can negatively impact the crusher’s performance. Regular inspections and replacements can help prevent this.
- Lubricate moving parts: Lubricating the crusher’s moving parts can help reduce friction and wear, leading to better performance and longer lifespan.
- Keep the crusher clean: A clean crusher is less likely to experience breakdowns. Regularly cleaning the crusher can help prevent dust buildup, which can cause damage to the machine.
Safety Considerations
Crushers can be dangerous if not operated and maintained properly. Here are some safety considerations to keep in mind:
- Always wear appropriate personal protective equipment (PPE): PPE such as hard hats, safety glasses, and earplugs can help protect workers from hazards such as falling debris and loud noises.
- Follow lockout/tagout procedures: Before performing any maintenance or repairs on the crusher, ensure that all energy sources are locked out and tagged out to prevent accidental startup.
- Train workers on proper operation and maintenance: Workers who operate and maintain the crusher should receive proper training to ensure they understand how to operate the machine safely and effectively.
By following proper maintenance and safety strategies, crushers can operate smoothly and safely, leading to increased productivity and reduced downtime.
Technological Advancements
Automation and Control
Crushers have come a long way from their early days of being manually operated. With the advent of automation and control systems, crushers have become more efficient and reliable. Automation has enabled crushers to operate at their peak efficiency, reducing downtime and increasing productivity. Control systems have made it possible to monitor and adjust crusher settings in real-time, ensuring that the crusher is always operating at optimal levels.
One of the most significant advancements in crusher automation and control is the ability to remotely monitor and control crushers. This technology has made it possible to operate crushers from a remote location, reducing the need for on-site personnel. Remote monitoring and control systems allow operators to adjust crusher settings, monitor performance, and receive alerts in real-time, ensuring that any issues are addressed promptly.
Wear Material Developments
Wear materials are an essential component of crushers, as they are responsible for protecting the crusher from wear and tear. Over the years, significant advancements have been made in wear material development, resulting in longer-lasting and more durable materials.
One of the most significant developments in wear materials is the use of composite materials. Composite materials are made up of two or more materials with different properties, resulting in a material that is stronger and more durable than its individual components. Composite wear materials have been developed for use in crushers, resulting in longer-lasting and more durable wear components.
Another significant development in wear materials is the use of ceramics. Ceramic wear materials are extremely hard and wear-resistant, making them ideal for use in crushers. Ceramic wear components have been developed for use in crushers, resulting in longer-lasting and more durable wear components.
In conclusion, technological advancements in automation and control and wear material development have significantly improved the efficiency and reliability of crushers. These advancements have resulted in crushers that are more productive, have reduced downtime, and are more durable, ultimately resulting in cost savings for operators.