
Screw Conveyor Dryer: An Efficient Drying Solution
Screw Conveyor Dryer: An Efficient Drying Solution
A screw conveyor dryer is a type of industrial dryer that uses a screw conveyor to move material through the dryer. The screw conveyor is typically made of stainless steel and is used to transport the material from one end of the dryer to the other. The dryer itself is typically a long cylindrical drum that is heated from the outside, either with hot air or steam.
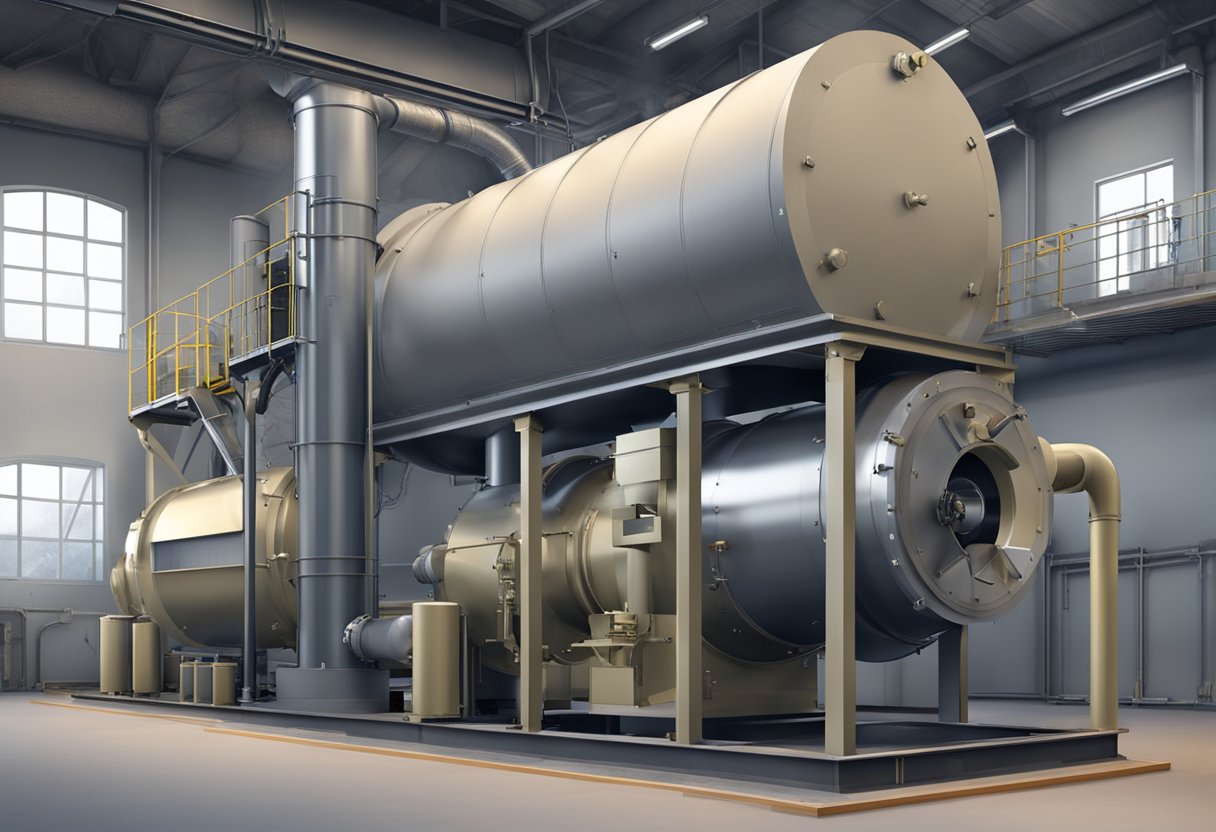
One of the key advantages of a screw conveyor dryer is its ability to handle a wide range of materials. Screw conveyor dryers can be used to dry materials ranging from food products to chemicals and pharmaceuticals. They are also widely used in the agricultural industry to dry grains, seeds, and other crops.
Overall, screw conveyor dryers are a reliable and efficient way to dry a wide range of materials. They are widely used across a variety of industries and are known for their versatility and ease of use.
Design Principles
Material Considerations
When designing a screw conveyor dryer, the material being processed should be taken into consideration. The material’s physical and chemical properties will impact the design of the conveyor and the overall drying process. For example, materials with high moisture content may require a larger conveyor diameter to allow for adequate airflow and drying time. Materials that are abrasive or corrosive may require special coatings or materials for the conveyor components to prevent wear and damage.
Mechanical Specifications
The mechanical specifications of a screw conveyor dryer are crucial to its performance and longevity. The conveyor should be designed with a sturdy frame and bearings that can handle the load and stress of the drying process. The motor and drive system should be appropriately sized to ensure smooth and consistent operation. The conveyor should also be designed with easy access for maintenance and cleaning.
When selecting the mechanical components for the screw conveyor dryer, it is important to consider factors such as the required throughput, the material being processed, and the desired drying temperature and time. These factors will impact the choice of conveyor diameter, pitch, and speed, as well as the motor and drive system.
Overall, the design of a screw conveyor dryer should be tailored to the specific material and process requirements to ensure optimal performance and efficiency.
Types of Screw Conveyor Dryers
Screw conveyor dryers are a popular type of dryer used in various industries for drying materials. They are efficient, easy to operate, and can handle a wide range of materials. There are two main types of screw conveyor dryers: direct heat dryers and indirect heat dryers.
Direct Heat Dryers
Direct heat dryers are also known as convective dryers. They work by passing hot air or gas through the material being dried. The hot air or gas is generated by a burner or heater, and it is forced through the material by the screw conveyor. As the material moves through the dryer, it is heated and dried.
Direct heat dryers are ideal for drying materials that can withstand high temperatures, such as minerals, chemicals, and food products. They are also used for drying materials that require rapid drying, such as wood chips and sawdust.
Indirect Heat Dryers
Indirect heat dryers are also known as contact dryers. They work by heating the walls of the dryer, which in turn transfer heat to the material being dried. The screw conveyor moves the material through the dryer, and as it comes into contact with the heated walls, it is dried.
Indirect heat dryers are ideal for drying materials that are sensitive to high temperatures, such as pharmaceuticals and food products. They are also used for drying materials that require gentle drying, such as biomass and organic materials.
Overall, both direct heat and indirect heat screw conveyor dryers have their own advantages and disadvantages, and the choice between the two depends on the specific requirements of the application.
Operating Mechanism
Conveying Process
Screw conveyor dryer is a type of dryer that uses a screw conveyor to move materials from one end to the other. The conveying process of a screw conveyor dryer involves the rotation of a helical screw blade, which is mounted on a shaft inside a cylindrical casing. As the screw rotates, it moves the material along the length of the dryer.
The screw conveyor dryer is designed to handle a wide range of materials, including powders, granules, and pastes. The size and shape of the screw blade can be customized to suit the specific characteristics of the material being dried.
Drying Process
The drying process of a screw conveyor dryer involves the transfer of heat from a heating medium to the material being dried. The heating medium can be steam, hot water, or hot air, depending on the requirements of the process.
The material being dried is conveyed through the dryer by the screw blade, and as it moves along the length of the dryer, it comes into contact with the heating medium. The heat is transferred from the heating medium to the material, causing the moisture to evaporate.
The design of the screw conveyor dryer is such that the material being dried is exposed to the heating medium for a longer period of time, which ensures that the moisture is completely evaporated. The dried material is then discharged from the dryer at the other end.
In summary, the operating mechanism of a screw conveyor dryer involves the movement of material through a rotating screw blade, which conveys the material along the length of the dryer. The material is exposed to a heating medium, which transfers heat to the material, causing the moisture to evaporate. The design of the dryer ensures that the material is exposed to the heating medium for a sufficient amount of time to ensure complete drying.
Thermal Efficiency
Heat Transfer Methods
Screw conveyor dryers are known for their high thermal efficiency due to their unique design, which enables efficient heat transfer. Heat is transferred to the material being dried through conduction, convection, and radiation.
Conduction involves the transfer of heat through direct contact between the material and the heated surface of the screw conveyor. The screw conveyor’s large surface area ensures that there is a high rate of heat transfer, making it an efficient method of drying.
Convection occurs when hot air is circulated around the material being dried. The screw conveyor’s design allows for the efficient circulation of hot air, ensuring that the material is evenly heated and dried.
Radiation involves the transfer of heat through electromagnetic waves. The screw conveyor’s design ensures that the material is exposed to a high level of radiation, resulting in efficient drying.
Energy Recovery Systems
Screw conveyor dryers can also be equipped with energy recovery systems, which further increase their thermal efficiency. These systems capture and reuse the heat generated during the drying process, reducing the amount of energy required to operate the dryer.
One common energy recovery system is a heat exchanger, which captures the heat from the exhaust air and uses it to preheat the incoming air. This results in significant energy savings and increased thermal efficiency.
Another energy recovery system is a thermal oxidizer, which captures the heat from the exhaust air and uses it to combust volatile organic compounds (VOCs) emitted during the drying process. This not only increases the thermal efficiency of the dryer but also reduces air pollution.
In conclusion, screw conveyor dryers are known for their high thermal efficiency due to their unique design and the ability to incorporate energy recovery systems. These systems result in significant energy savings and increased efficiency, making screw conveyor dryers a popular choice for industrial drying applications.
Material Handling
Feeding Systems
In screw conveyor dryers, the feeding system is a crucial component that determines the efficiency of the whole process. The feeding system should be designed to handle the material to be dried and deliver it to the dryer in a controlled manner. The most common feeding systems are volumetric and gravimetric feeders.
Volumetric feeders are suitable for materials that do not vary much in density, shape, and size. They work by measuring the volume of the material and delivering it to the dryer at a fixed rate. On the other hand, gravimetric feeders are more precise and can handle materials that vary in density, shape, and size. They work by measuring the weight of the material and adjusting the feed rate accordingly.
Discharge Methods
Once the material is dried, it needs to be discharged from the dryer. There are several methods for discharging the material, including screw conveyors, rotary valves, and airlocks. Screw conveyors are the most common method for discharging the material from the dryer. They are reliable, easy to maintain, and can handle a wide range of materials.
Rotary valves are another method for discharging the material. They work by rotating a valve to allow the material to flow out of the dryer. Rotary valves are suitable for materials that are prone to bridging or jamming. Airlocks are also commonly used for discharging the material. They work by creating a seal between the dryer and the downstream equipment to prevent air from entering the system.
In summary, the feeding system and discharge method are critical components of a screw conveyor dryer. The right design and selection of these components can significantly improve the efficiency and reliability of the drying process.
Performance Optimization
Process Control
Proper process control is essential for achieving optimal performance in screw conveyor dryers. The control system should be able to monitor and adjust the temperature, airflow, and feed rate to ensure that the material is dried uniformly and efficiently.
One effective way to optimize the drying process is to use a feedback control system that continuously measures the moisture content of the material and adjusts the drying parameters accordingly. This can be achieved by installing sensors at various points in the dryer and using a control algorithm to adjust the process parameters in real-time.
Another important aspect of process control is to ensure that the material is conveyed through the dryer at a consistent rate. This can be achieved by using a variable frequency drive (VFD) to adjust the speed of the screw conveyor based on the feed rate of the material.
Maintenance Strategies
Regular maintenance is crucial for ensuring that screw conveyor dryers operate at peak performance. Some key maintenance strategies include:
- Lubrication: Proper lubrication of the bearings, seals, and other moving parts is essential for preventing wear and extending the life of the dryer.
- Inspection: Regular inspection of the dryer components can help identify potential issues before they become major problems. This can include checking for wear on the screw flights, inspecting the seals for leaks, and verifying that the drive system is functioning properly.
- Cleaning: Regular cleaning of the dryer can help prevent material buildup and ensure that the dryer operates efficiently. This can include cleaning the interior of the dryer, removing any debris from the screw conveyor, and inspecting the air handling system for any blockages or obstructions.
By implementing these maintenance strategies and optimizing the process control system, screw conveyor dryers can achieve optimal performance and efficiency.