
Gas Scrubber: A Comprehensive Guide to Understanding Its Function and Importance in Industrial Processes
Gas Scrubber: A Comprehensive Guide to Understanding Its Function and Importance in Industrial Processes
Gas scrubber are an essential component of many industrial processes. They are used to remove harmful pollutants, such as sulfur dioxide and nitrogen oxides, from exhaust gases before they are released into the atmosphere. The scrubbing process involves passing the exhaust gas through a liquid, which absorbs the pollutants. The cleaned gas is then released into the atmosphere, while the liquid containing the pollutants is treated or disposed of.
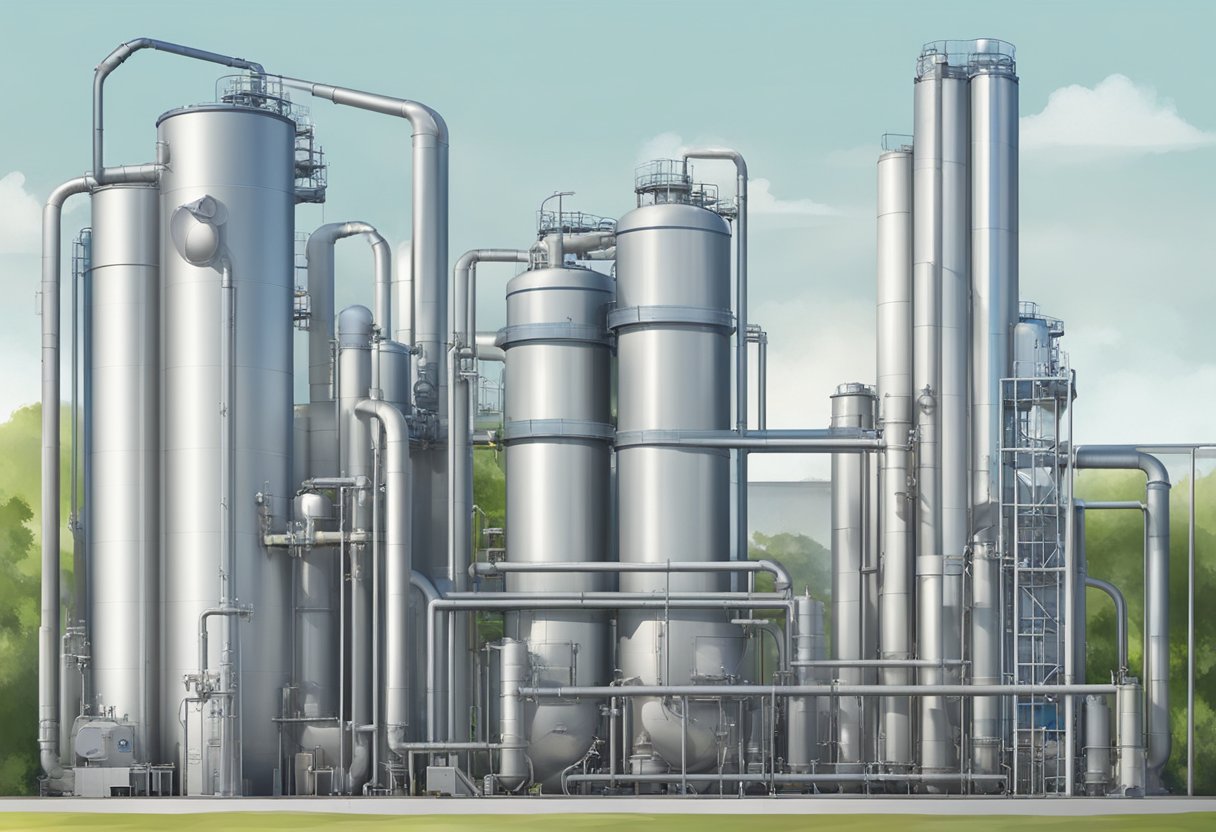
Gas scrubbers are used in a wide range of industries, including power generation, chemical processing, and oil and gas production. They are particularly important in industries that produce large amounts of pollutants, as they help to reduce the environmental impact of these activities. Gas scrubbers can also help companies to comply with environmental regulations, which often have strict limits on the amount of pollutants that can be released into the atmosphere.
Fundamentals of Gas Scrubbing

Gas scrubbing is a process that involves removing pollutants from industrial exhaust gases before they are released into the atmosphere. This process is critical to protecting the environment and ensuring compliance with air quality regulations. The fundamental principle behind gas scrubbing is the use of a scrubbing solution to absorb the pollutants from the gas stream.
The scrubbing solution can be a liquid or a solid, depending on the nature of the pollutants. The most commonly used scrubbing solutions are water, alkaline solutions, and acids. The choice of scrubbing solution depends on the type of pollutant and the desired level of removal.
Gas scrubbers can be categorized into two main types: wet scrubbers and dry scrubbers. Wet scrubbers use a liquid scrubbing solution to remove pollutants from the gas stream, while dry scrubbers use a solid scrubbing material. Wet scrubbers are more commonly used because they are more effective in removing a wider range of pollutants.
The efficiency of gas scrubbing depends on several factors, including the type of scrubber, the scrubbing solution, the gas flow rate, and the pollutant concentration. To ensure optimal performance, it is essential to select the appropriate scrubber design and scrubbing solution for the specific application.
In summary, gas scrubbing is a critical process for removing pollutants from industrial exhaust gases. The choice of scrubbing solution and scrubber design depends on the nature of the pollutants and the desired level of removal. Proper selection and operation of gas scrubbers are essential to ensure compliance with air quality regulations and protect the environment.
Types of Gas Scrubbers
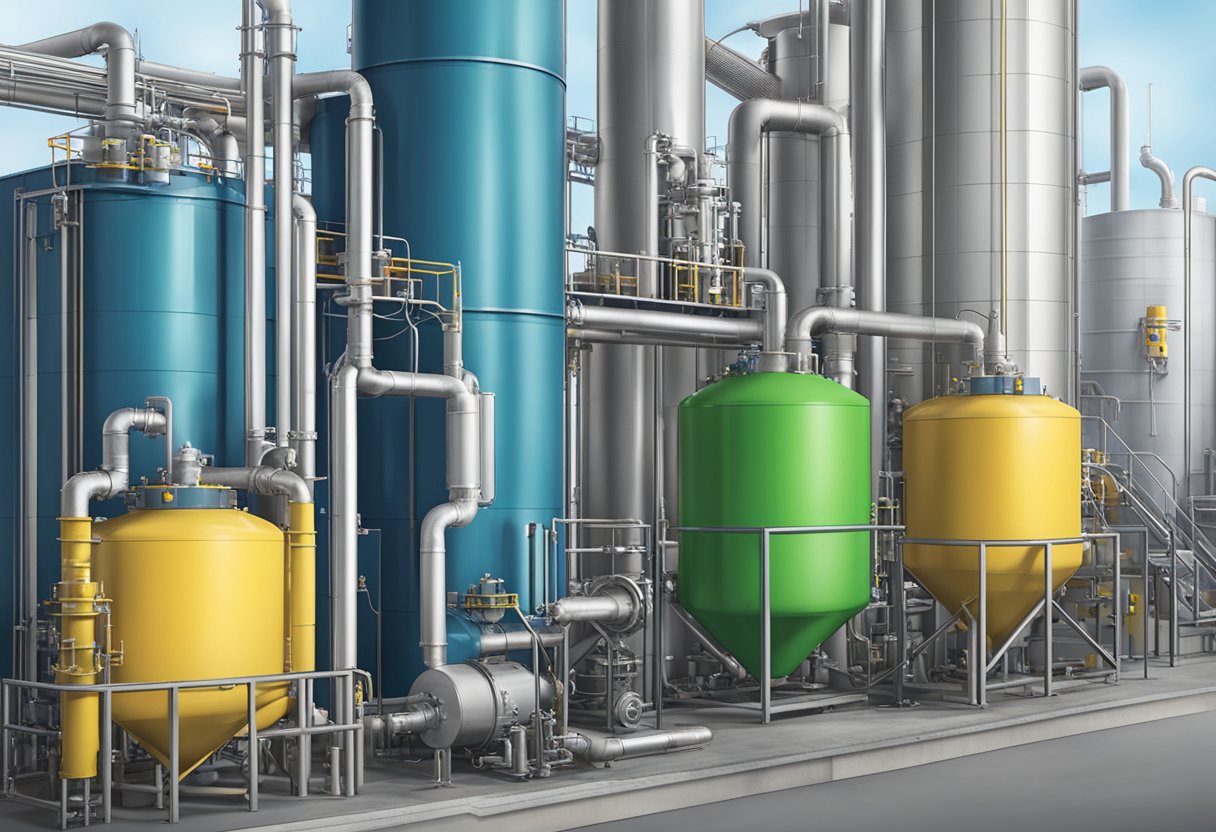
Gas scrubbers are essential in removing pollutants from industrial exhaust gases before they are released into the environment. There are different types of gas scrubbers, each with unique characteristics and applications. In this section, we will discuss the three main types of gas scrubbers: Wet Scrubbers, Dry Scrubbers, screw conveyor and Electrostatic Scrubbers.
Wet Scrubbers
Wet scrubbers are the most common type of gas scrubbers used in industrial applications. They use a liquid to remove pollutants from the gas stream by absorbing or dissolving them into the liquid. Wet scrubbers are effective in removing both particulate matter and gaseous pollutants. They are also versatile and can handle a wide range of pollutants and gas flow rates.
Wet scrubbers can be further classified into various types based on their design and operation. Some of the popular types of wet scrubbers include:
- Venturi Scrubbers
- Spray Tower Scrubbers
- Packed Bed Scrubbers
- Impingement Plate Scrubbers
Dry Scrubbers
Dry scrubbers use a dry sorbent material to remove pollutants from the gas stream. The sorbent material can be in the form of pellets, granules, or powder. Dry scrubbers are effective in removing acid gases such as sulfur dioxide and hydrogen chloride. They are also suitable for applications where the gas flow rate is low, and the pollutants are in low concentrations.
Some of the common types of dry scrubbers include:
- Spray Dry Scrubbers
- Circulating Fluidized Bed Scrubbers
- Dry Sorbent Injection Systems
Electrostatic Scrubbers
Electrostatic scrubbers use an electric field to charge the particles in the gas stream. The charged particles are then collected on an oppositely charged surface, such as a plate or a wire. Electrostatic scrubbers are effective in removing fine particulate matter and can handle high gas flow rates.
Electrostatic scrubbers can be further classified into two types:
- Plate-Type Electrostatic Precipitators
- Tubular-Type Electrostatic Precipitators
In conclusion, gas scrubbers play a crucial role in reducing air pollution from industrial activities. By understanding the different types of gas scrubbers available, industries can choose the most suitable option for their specific needs and applications.
Components and Design
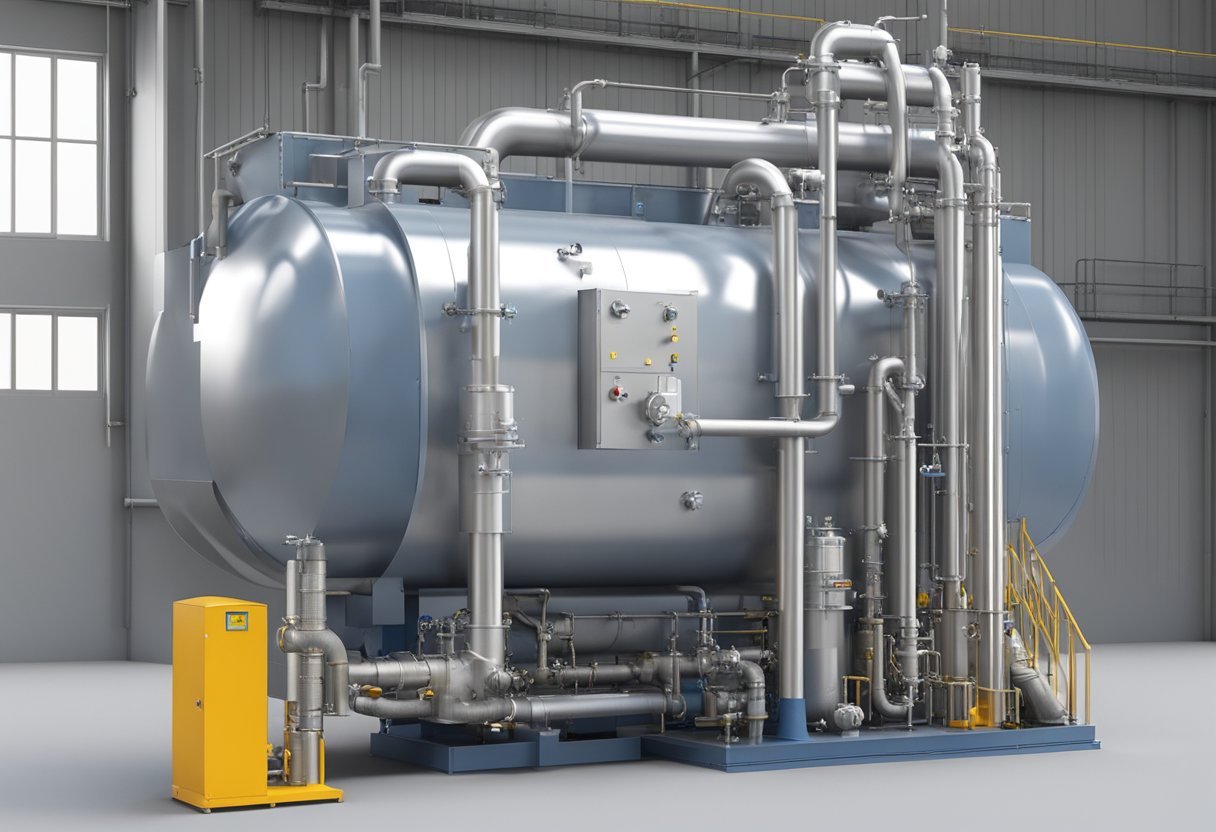
Gas scrubbers are designed to remove pollutants from industrial exhaust gases. They consist of several components that work together to achieve this goal.
Absorption Tower
The absorption tower is the main component of the gas scrubber. It is a tall cylindrical vessel that contains the scrubbing liquid. The exhaust gas enters the bottom of the tower and flows upward through the liquid. The liquid absorbs the pollutants from the gas, and the clean gas exits the top of the tower.
Packing Material
The packing material is used to increase the surface area of the scrubbing liquid. The more surface area there is, the more effective the scrubbing process will be. The packing material is typically made of plastic, metal, or ceramic and is placed inside the absorption tower.
Mist Eliminators
Mist eliminators are used to remove any liquid droplets that may be carried over with the clean gas. They are placed at the top of the absorption tower and are designed to capture any liquid droplets before they can exit the tower.
Ductwork and Fans
Ductwork and fans are used to move the exhaust gas through the scrubber and out into the atmosphere. The fans are typically located at the top of the absorption tower and are used to create a negative pressure inside the tower. This negative pressure helps to draw the exhaust gas through the scrubber and out into the atmosphere.
In summary, gas scrubbers are designed to remove pollutants from industrial exhaust gases. They consist of several components, including the absorption tower, packing material, mist eliminators, and ductwork and fans. Each component plays a crucial role in the scrubbing process, and they work together to achieve a clean and safe working environment.
Chemical Processes Involved
Absorption
Gas scrubbers use various chemical processes to remove pollutants and contaminants from gas streams. One of the most common processes is absorption, which involves dissolving the pollutants into a liquid solvent. The solvent is typically a liquid that has a high affinity for the pollutants, such as water or an organic solvent.
During absorption, the gas stream is passed through a liquid stream, which allows the pollutants to dissolve into the liquid. The liquid is then separated from the gas stream, and the pollutants are removed from the liquid using various techniques such as distillation or evaporation.
Adsorption
Another common process used in gas scrubbers is adsorption. This process involves the use of a solid material, called an adsorbent, to capture pollutants from the gas stream. The adsorbent has a high surface area and a strong affinity for the pollutants, allowing it to capture and hold the pollutants on its surface.
During adsorption, the gas stream is passed through a bed of the adsorbent material, which captures the pollutants. The adsorbent is then removed from the gas stream, and the pollutants are removed from the adsorbent using various techniques such as heating or washing.
Chemical Reaction
Gas scrubbers can also use chemical reactions to remove pollutants from gas streams. This process involves the use of chemicals that react with the pollutants, converting them into less harmful substances. The chemicals used in these reactions are typically chosen based on their ability to react with specific pollutants.
During a chemical reaction, the gas stream is passed through a chamber containing the reactive chemicals. The pollutants react with the chemicals, forming less harmful substances. The gas stream is then passed through a series of filters to remove any remaining pollutants.
Overall, gas scrubbers use a variety of chemical processes to remove pollutants from gas streams. These processes are effective at removing a wide range of pollutants and can be tailored to specific applications.
Applications and Industries
Air Pollution Control
Gas scrubbers have been widely used in air pollution control applications to remove harmful pollutants from industrial exhaust gases. These pollutants include sulfur dioxide, nitrogen oxides, and particulate matter. Gas scrubbers have proven to be effective in reducing emissions and meeting regulatory requirements.
Chemical Processing
In the chemical processing industry, gas scrubbers are used to remove impurities and contaminants from process gases. This helps to ensure product quality and prevent equipment damage. Gas scrubbers are commonly used in the production of fertilizers, petrochemicals, and other chemicals.
Oil and Gas
Gas scrubbers are also used in the oil and gas industry to remove impurities from natural gas and other process gases. This helps to ensure the quality of the gas and prevent damage to downstream equipment. Gas scrubbers are commonly used in gas processing plants, refineries, and offshore platforms.
Gas scrubbers offer a reliable and effective solution for a variety of industrial applications. They can be customized to meet specific process requirements and are available in a range of sizes and configurations. With their proven track record of success, gas scrubbers are a valuable tool for improving process efficiency and reducing environmental impact.
Performance Metrics
Efficiency
Efficiency is a key performance metric for gas scrubbers. It measures the ability of the scrubber to remove contaminants from the gas stream. The efficiency of a gas scrubber is influenced by various factors such as the type of scrubbing media, gas flow rate, scrubbing liquid flow rate, and temperature.
Gas scrubbers with high efficiency are desirable as they can remove a high percentage of contaminants from the gas stream. The efficiency of gas scrubbers can be measured using various methods such as gravimetric analysis, gas chromatography, and spectrophotometry.
Pressure Drop
Pressure drop is another important performance metric for gas scrubbers. It measures the resistance of the scrubber to gas flow. A high-pressure drop can result in reduced gas flow rate and increased energy consumption.
The pressure drop in a gas scrubber is influenced by various factors such as the type of scrubbing media, gas flow rate, scrubbing liquid flow rate, and temperature. Gas scrubbers with low pressure drop are desirable as they can reduce energy consumption and increase gas flow rate.
Operational Costs
Operational costs are an important consideration when selecting a gas scrubber. The operational costs of a gas scrubber include the cost of scrubbing media, scrubbing liquid, energy consumption, maintenance, and disposal of waste.
Gas scrubbers with low operational costs are desirable as they can reduce the overall cost of gas treatment. The operational costs of a gas scrubber can be minimized by selecting an appropriate scrubbing media, optimizing the gas flow rate and scrubbing liquid flow rate, and implementing a regular maintenance schedule.
In conclusion, gas scrubbers are an important technology for removing contaminants from gas streams. The performance of gas scrubbers can be evaluated using various metrics such as efficiency, pressure drop, and operational costs. By selecting a gas scrubber with high efficiency, low pressure drop, and low operational costs, the overall cost of gas treatment can be minimized.
Maintenance and Safety
Routine Checks
Regular maintenance is crucial to ensure the proper functioning of gas scrubbers. Routine checks should be carried out at fixed intervals to prevent any potential issues. The following checks should be performed daily:
- Check the scrubber’s inlet and outlet valves to ensure that they are functioning correctly.
- Inspect the scrubber’s packing material and replace it if it is damaged or worn out.
- Check the scrubber’s liquid level and add more liquid if necessary.
- Inspect the scrubber’s blower and motor to ensure that they are functioning correctly.
Safety Precautions
Gas scrubbers can be dangerous if not handled properly. It is essential to follow safety precautions to prevent accidents. The following precautions should be taken:
- Wear protective clothing, including gloves and goggles, when handling chemicals.
- Ensure that the scrubber is properly grounded to prevent electrical shocks.
- Never open the scrubber while it is in operation.
- Keep the scrubber away from heat sources and flammable materials.
Troubleshooting
Despite regular maintenance, gas scrubbers may encounter issues. Troubleshooting should be performed to identify and resolve any problems. The following steps should be taken:
- Check the scrubber’s packing material and replace it if it is damaged or worn out.
- Inspect the scrubber’s blower and motor to ensure that they are functioning correctly.
- Check the scrubber’s liquid level and add more liquid if necessary.
- Inspect the scrubber’s inlet and outlet valves to ensure that they are functioning correctly.
In case of any significant issues, it is recommended to seek professional help.