
Secadores Rotatorios: A Comprehensive Guide to Rotary Dryers
Secadores Rotatorios: A Comprehensive Guide to Rotary Dryers
Rotary dryers, also known as secadores rotatorios in Spanish, are industrial machines used for drying various materials. They are commonly used in the mining, chemical, and agricultural industries to dry materials such as minerals, fertilizers, and grains. The design of a rotary dryer involves a rotating drum that is heated with a direct or indirect heat source, allowing for efficient drying of the material inside.
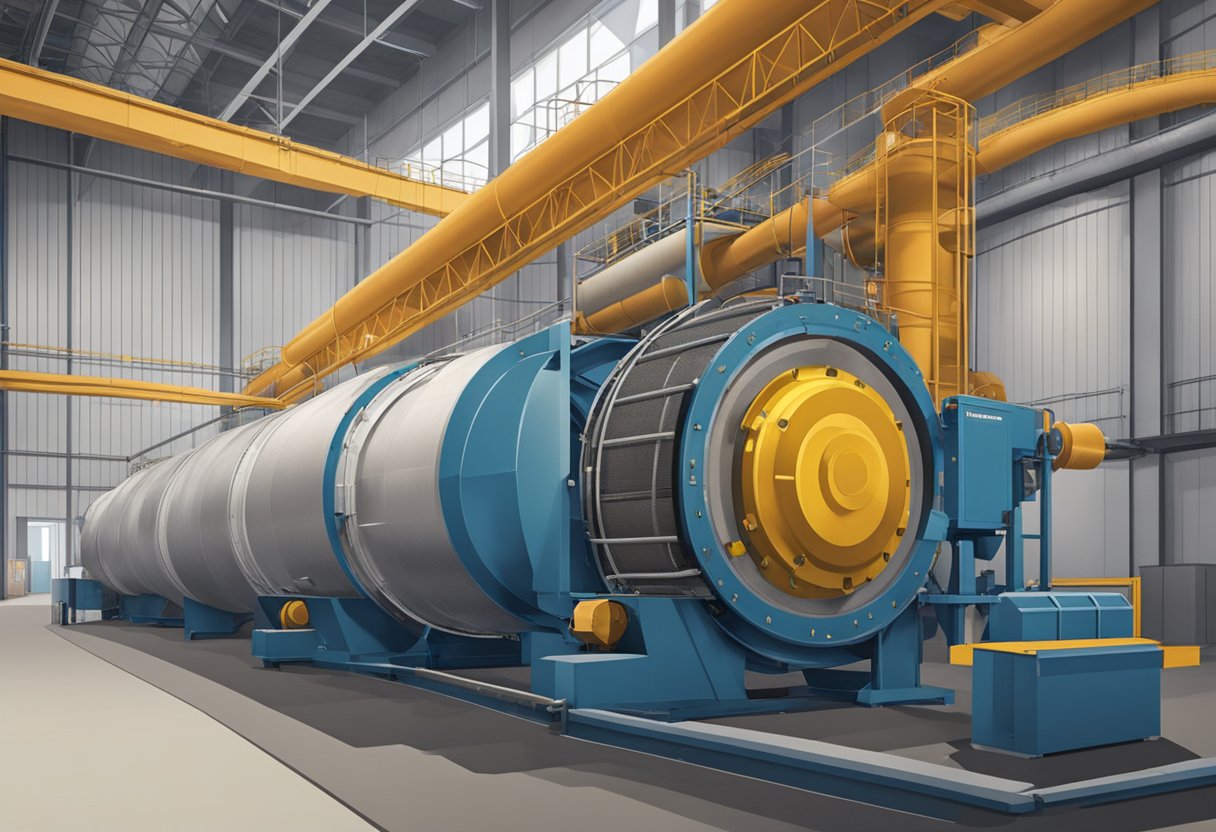
One of the advantages of using a rotary dryer is the ability to process large quantities of material at once. The rotating drum allows for even and consistent drying of the material, reducing the need for manual labor and increasing productivity. Additionally, the design of a rotary dryer allows for the material to be dried at a lower temperature than other drying methods, reducing the risk of damage or degradation to the material.
While rotary dryers have many benefits, they also require proper maintenance and operation to ensure optimal performance. Regular cleaning and inspection of the drum and heat source are necessary to prevent buildup and ensure efficient drying. Proper selection of the heat source and control of the drying temperature are also important factors in achieving the desired drying results.
Fundamentals of Rotary Dryers
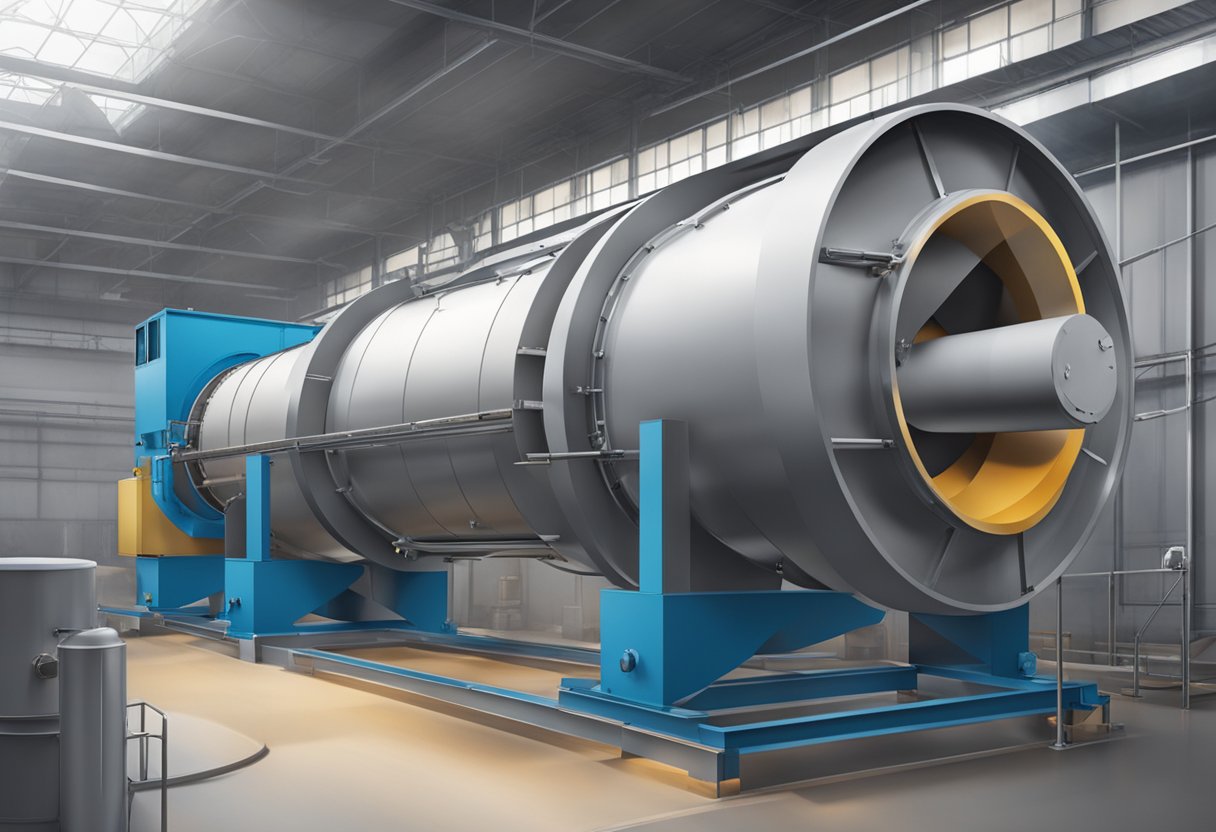
Rotary dryers are a type of industrial dryer that are used to remove moisture from a material by exposing it to a direct or indirect heat source. They are commonly used in the chemical, mineral, and food processing industries.
How Rotary Dryers Work
Rotary dryers work by tumbling a material through a rotating drum. The material is fed into one end of the drum and as it moves through the drum, it is heated by a direct or indirect heat source. The moisture in the material is evaporated and exits the dryer through a vent at the other end of the drum.
Types of Rotary Dryers
There are several types of rotary dryers, including direct heat rotary dryers, indirect heat rotary dryers, steam tube rotary dryers, and rotary vacuum dryers. Each type has its own advantages and disadvantages, depending on the material being dried and the desired end product.
Advantages of Rotary Dryers
Rotary dryers offer several advantages over other types of dryers. They are able to handle a wide range of materials and can be used for both small and large-scale drying applications. They are also energy-efficient and can be designed to operate in a closed-loop system, which reduces the amount of heat and moisture lost during the drying process.
Design and Construction
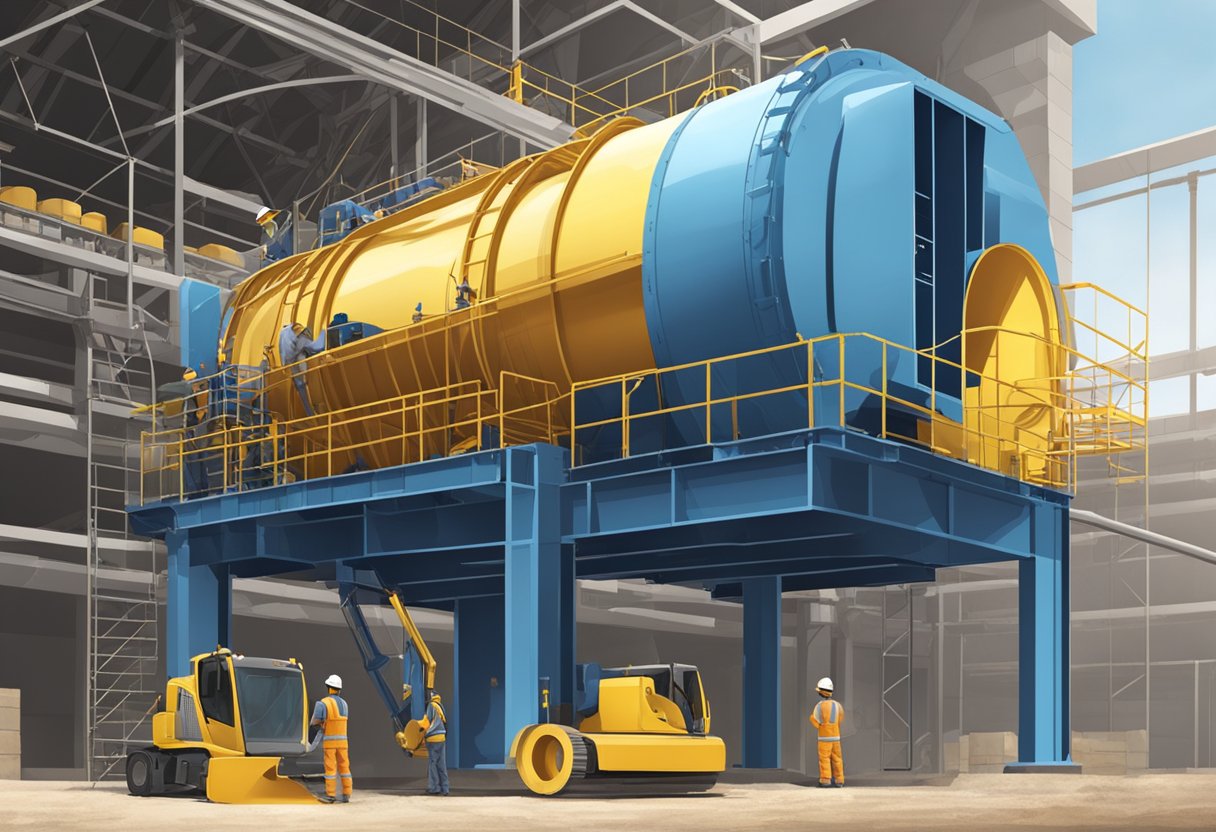
Materials and Components
Rotary dryers are typically composed of a rotating cylindrical drum, which is supported by two or more trunnion wheels. The drum is usually made of steel and can vary in diameter and length depending on the application. The drum is lined with refractory material to protect it from the high temperatures generated during the drying process.
The drum is driven by a motor through a chain and sprocket system. The motor is typically located on the discharge end of the dryer. The inlet and outlet are sealed with rotary seals, which prevent air from entering or escaping the system.
Drum Design
The drum is designed to maximize the contact between the material being dried and the hot gas flowing through the dryer. The drum is typically inclined slightly from the inlet to the outlet end to facilitate the movement of the material through the system. The drum is also equipped with flights, which lift and cascade the material through the hot gas stream, ensuring that every particle is exposed to the heat.
Air Flow Configuration
The hot gas flows counter-current to the material being dried, which maximizes the heat transfer efficiency. The gas is typically generated by a burner located in the discharge end of the dryer. The hot gas is then drawn through the system by an induced draft fan located on the inlet end of the dryer. The gas is typically recirculated through the system to maximize the thermal efficiency and reduce the emissions.
In summary, rotary dryers are composed of a rotating cylindrical drum, which is driven by a motor and supported by trunnion wheels. The drum is designed to maximize the contact between the material being dried and the hot gas flowing through the dryer. The hot gas flows counter-current to the material being dried, and the system is designed to maximize the thermal efficiency and reduce the emissions.
Operating Principles
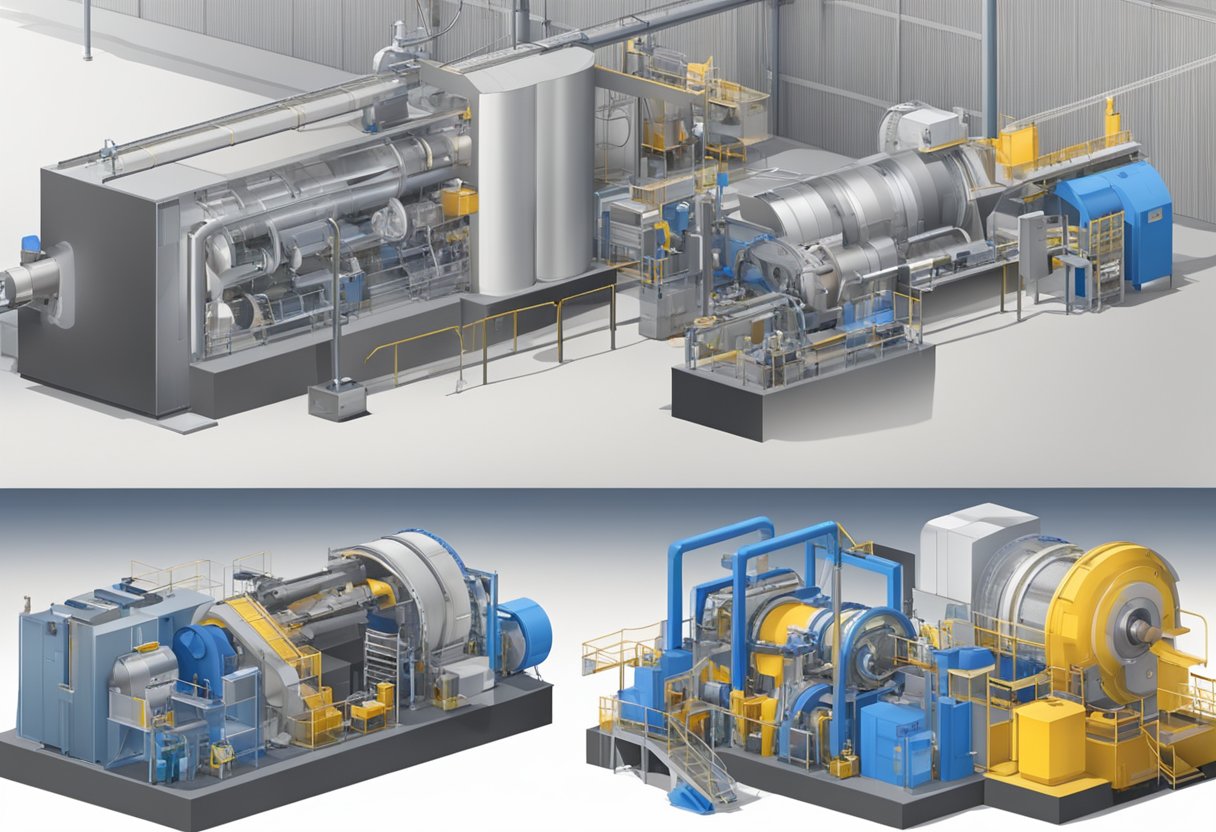
Secadores rotatorios, or rotary dryers, are commonly used in industrial settings to dry and process various materials. They operate on the principle of direct contact between the material being dried and the drying medium, typically air or gas.
Heat Transfer
The heat transfer mechanism in a rotary dryer is primarily convection. Hot air or gas is introduced into the dryer and flows through the material bed, transferring heat to the wet material. The heat causes the moisture in the material to evaporate, which is then carried away by the drying medium.
Heat transfer in a rotary dryer can also occur through conduction and radiation. Conduction occurs when the material comes into direct contact with the hot surfaces of the dryer, while radiation occurs when the material absorbs heat from the surrounding environment.
Material Movement
The movement of material in a rotary dryer is achieved through the rotation of the dryer cylinder. As the cylinder rotates, the material is lifted and cascades through the drying medium, ensuring even exposure to the drying medium and promoting efficient drying.
The speed of rotation and the angle of inclination of the dryer cylinder can be adjusted to control the residence time of the material in the dryer and the degree of agitation. This allows for precise control over the drying process and ensures optimal drying efficiency.
In conclusion, understanding the operating principles of secadores rotatorios is essential for ensuring efficient and effective drying of various materials in industrial settings. By controlling the heat transfer mechanism and material movement, rotary dryers can be optimized for specific applications and provide reliable and consistent drying results.
Applications and Uses
Industrial Processes
Secadores rotatorios, or rotary dryers, have a wide range of applications in various industries. They are commonly used for drying materials in the chemical, food processing, and pharmaceutical industries. Rotary dryers are also used in the mining and mineral processing industries to dry materials such as ores, coal, and sand.
In the chemical industry, rotary dryers are used to dry chemicals and compounds before they are processed further. In the food processing industry, rotary dryers are used to dry food products such as fruits, vegetables, and meat. The pharmaceutical industry uses rotary dryers to dry active ingredients and other materials before they are formulated into medications.
Rotary dryers are also used in the environmental industry to dry sludge from wastewater treatment plants. This helps reduce the volume of sludge and makes it easier to dispose of.
Agricultural Sector
In the agricultural sector, rotary dryers are commonly used to dry crops such as corn, soybeans, and wheat. This helps farmers preserve their crops and prevent spoilage. Rotary dryers are also used to dry animal feed, such as alfalfa and grass, which helps preserve the nutritional value of the feed.
In addition, rotary dryers are used to dry manure from livestock, which helps reduce the odor and makes it easier to handle. This dried manure can also be used as a fertilizer.
Overall, secadores rotatorios have a wide range of applications and uses in various industries. They are effective at drying materials quickly and efficiently, which helps improve productivity and reduce waste.
Efficiency and Performance
Energy Consumption
Secadores rotatorios are known for their efficiency in drying materials quickly and effectively. One important factor that contributes to their efficiency is their energy consumption. These machines are designed to use minimal energy while still providing optimal drying performance. This means that they can help reduce energy costs and minimize environmental impact.
To further improve energy efficiency, some secadores rotatorios are equipped with advanced control systems that allow for precise temperature and airflow control. This helps to ensure that the drying process is optimized for maximum efficiency and performance.
Optimization Techniques
In addition to energy consumption, there are several optimization techniques that can be used to improve the performance of secadores rotatorios. One such technique is the use of advanced sensors and monitoring systems that can track the progress of the drying process in real-time. This allows for quick adjustments to be made to the temperature and airflow to ensure that the drying process is optimized for maximum efficiency.
Another optimization technique is the use of specialized coatings and materials that can help improve heat transfer and reduce energy loss. These coatings and materials are designed to withstand the high temperatures and harsh conditions of the drying process, while still providing optimal performance and efficiency.
Overall, secadores rotatorios are highly efficient and effective machines for drying a wide range of materials. By using advanced control systems and optimization techniques, these machines can help reduce energy costs and minimize environmental impact, while still providing optimal performance and efficiency.
Maintenance and Safety
Routine Maintenance
Secadores rotatorios are sturdy machines that can operate for years without any issues if they are maintained properly. The routine maintenance of secadores rotatorios includes cleaning the machine after every use, inspecting the machine for any signs of wear and tear, and replacing any damaged parts.
It is important to keep the machine clean to prevent any buildup of debris or dust, which can lead to reduced efficiency and even damage to the machine. The inspection of the machine should be done regularly to identify any potential issues before they become major problems. Replacing damaged parts promptly can save time and money in the long run.
Safety Measures
Secadores rotatorios can be dangerous if not operated properly. It is important to follow all safety guidelines provided by the manufacturer. Some of the safety measures that should be taken include wearing personal protective equipment (PPE) such as gloves, goggles, and masks, ensuring that the machine is properly grounded, and keeping the machine away from any flammable materials.
Additionally, it is important to never tamper with any safety features of the machine, such as guards or interlocks. These features are in place to prevent accidents and should always be kept in working order.
Troubleshooting
Despite routine maintenance and following safety measures, secadores rotatorios may still experience issues. Troubleshooting can help identify and resolve any problems with the machine. Some common issues include overheating, vibration, and noise.
If any issues arise, it is important to refer to the manufacturer’s manual for troubleshooting steps. If the issue cannot be resolved, it is recommended to contact a professional for assistance. Attempting to fix the machine without proper knowledge and training can be dangerous and may cause further damage to the machine.
Control Systems
Automation
Secadores rotatorios often come equipped with automation systems that control the drying process. These systems can help optimize the drying process by adjusting the temperature, airflow, and rotation speed of the drum based on the moisture content of the material being dried.
The automation system can also help reduce the risk of human error and improve the consistency of the drying process. Additionally, some systems can be programmed to stop the dryer automatically if certain parameters, such as temperature or airflow, exceed safe levels.
Sensors and Monitoring
Sensors and monitoring systems are often used in secadores rotatorios to measure key parameters such as temperature, humidity, and airflow. These sensors can help ensure that the drying process is running at optimal conditions and can provide real-time feedback to the automation system.
Some monitoring systems can also detect potential issues such as blockages or overheating and alert the operator to take corrective action. This can help prevent costly downtime and ensure that the dryer is operating safely and efficiently.
Overall, the control systems in secadores rotatorios can help optimize the drying process, improve consistency, and reduce the risk of human error. By utilizing automation and monitoring systems, operators can ensure that the dryer is running at optimal conditions and can quickly detect and correct any issues that arise.
Environmental Impact
Emissions Control
Secadores rotatorios, or rotary dryers, have a significant environmental impact due to their emissions. The drying process requires high temperatures, which can result in the release of harmful gases such as nitrogen oxides, carbon monoxide, and volatile organic compounds. However, manufacturers have implemented various measures to control these emissions.
One of the most common methods is the use of combustion technology that reduces the amount of fuel consumed and emissions released. Additionally, some manufacturers use regenerative thermal oxidizers (RTOs) to control emissions. RTOs are devices that destroy pollutants in exhaust gases by oxidizing them at high temperatures.
Sustainability Practices
Sustainability is a growing concern for many industries, including the manufacturing of secadores rotatorios. Manufacturers have implemented various sustainability practices to reduce their environmental impact.
One such practice is the use of renewable energy sources such as solar and wind power to reduce the carbon footprint of the manufacturing process. Additionally, manufacturers have implemented recycling programs to reduce waste and conserve resources.
Furthermore, some manufacturers have implemented water conservation practices in their manufacturing processes. For example, they use closed-loop systems that recycle water and reduce the amount of water used in the manufacturing process.
In conclusion, while secadores rotatorios have a significant environmental impact, manufacturers have implemented various measures to control emissions and reduce their carbon footprint. By implementing sustainability practices and using renewable energy sources, manufacturers can further reduce their environmental impact.
Market Trends and Demands
Secadores rotatorios have been gaining popularity in recent years due to their efficiency and versatility. The market demand for these dryers has been steadily increasing, especially in the chemical, food, and pharmaceutical industries.
One of the main trends in the market is the demand for customized secadores rotatorios that can meet specific requirements of the customers. Manufacturers are focusing on designing and producing dryers that can handle different types of materials and produce the desired quality of the end product.
Another trend in the market is the adoption of advanced technologies in the manufacturing process of secadores rotatorios. This has resulted in the production of dryers that are more energy-efficient, have a longer lifespan, and require less maintenance.
The demand for secadores rotatorios is also being driven by the increasing need for sustainable and eco-friendly solutions. Manufacturers are incorporating features such as waste heat recovery systems and low-emission burners to reduce the environmental impact of the dryers.
Overall, the market for secadores rotatorios is expected to continue growing in the coming years due to the increasing demand for efficient and sustainable drying solutions.
Case Studies
Several case studies have been conducted to determine the effectiveness of rotary dryers in various industries. Here are a few examples:
Case Study 1: Chemical Industry
A chemical company was facing a challenge of drying a high-viscosity material that had a tendency to stick to the dryer walls, leading to uneven drying. The company decided to use a rotary dryer with a specially designed internal flighting system. The system included flights that lifted and showered the material, ensuring even drying. The result was a consistent and high-quality product that met the company’s specifications.
Case Study 2: Food Industry
A food processing company was looking for a way to reduce the moisture content of a high-fat food product without compromising its quality. The company opted for a rotary dryer with a co-current flow pattern, which allowed for efficient heat transfer and reduced the risk of overheating the product. The result was a product with the desired moisture content and improved shelf life.
Case Study 3: Mining Industry
A mining company needed to dry a high-moisture ore to improve its handling and transportability. The company used a rotary dryer with a counter-current flow pattern, which allowed for efficient moisture removal and reduced the risk of material sticking to the dryer walls. The result was a dry and free-flowing material that was easier to handle and transport.
Overall, these case studies demonstrate the versatility and effectiveness of rotary dryers in a variety of industries. By choosing the right type of dryer and optimizing its design, companies can achieve their desired drying results and improve their product quality.
Future Developments
Secadores rotatorios have been widely used in various industries due to their efficiency and reliability. However, there is always room for improvement and innovation in this field.
One area of future development is the use of advanced materials for the construction of the dryer drum. The use of high-strength and heat-resistant materials can significantly increase the durability and lifespan of the dryer, resulting in lower maintenance costs and increased productivity.
Another area of development is the implementation of advanced control systems. By integrating sensors and automation technology, the dryer can be optimized for energy efficiency and product quality. This can lead to significant cost savings and improved product consistency.
Furthermore, research is being conducted to explore the use of renewable energy sources to power secadores rotatorios. Solar and wind power can be used to generate electricity, which can be used to operate the dryer. This can reduce the reliance on fossil fuels and lower the carbon footprint of the drying process.
Overall, the future of secadores rotatorios looks promising, with advancements in materials, control systems, and renewable energy sources set to improve their efficiency and sustainability.